Cas d’usage
Comment nos membres utilisent-ils la technologie de l’UAO et comment cela contribue à la valeur de l’entreprise
—
Si vous êtes intéressé par le lancement d’un projet avec UAO TECHNOLOGY et que vous souhaitez bénéficier d’un soutien, n’hésitez pas à nous contacter !
ExxonMobil
Défi
Adopter une plate-forme ouverte pour ne pas être lié à un seul fournisseur
Avantages
- Portabilité des applications utilisant les meilleurs composants logiciels de différents fournisseurs
- Exécution des applications de contrôle et de la logique de contrôle conformément aux normes d’automatisation ouvertes
- Réduire les délais d’ingénierie et de mise en service
- Stimuler l’innovation grâce à des logiciels éprouvés
- Amélioration continue grâce au remplacement des composants existants par des composants améliorés à l’aide d’interfaces standard.
Détails
- Utilisation du moteur d’exécution UAO dans le banc d’essai Open Process Automation (OPA) depuis 2018
- Exécution d’un déploiement sur le terrain pour remplacer les DCS/PLC existants par un système basé sur l’OPA
- Le projet comprend 800 points IO, 90+ boucles, UAO runtime + OPC UA
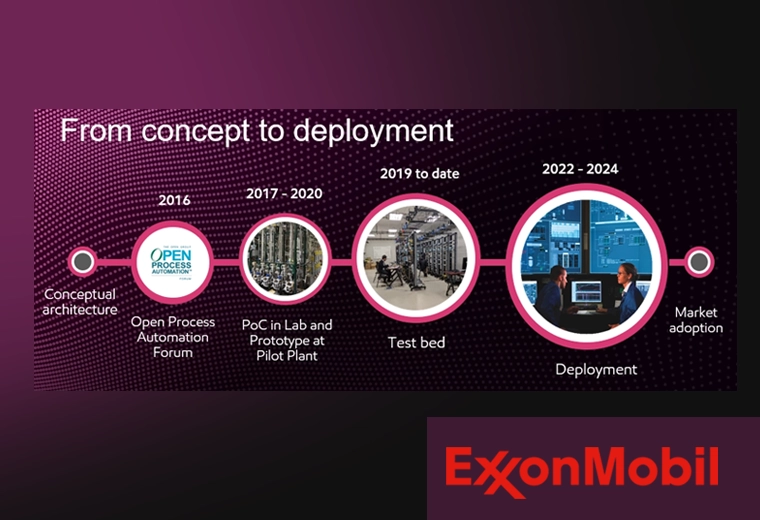
Gr3n
Défi
Augmenter facilement la production en utilisant des composants mécaniques/électriques/contrôleurs modulaires. Rester propriétaire de la propriété intellectuelle du logiciel et gagner en flexibilité en ce qui concerne le choix du fournisseur.
Avantages
- Ingénierie modulaire de l’automatisation de l’usine en fonction de la modularité du processus
- Réduction des coûts d’ingénierie lors de la mise à l’échelle du marché
- Amélioration du coût total de possession pour l’automatisation de leurs installations
- Nouvelles voies de protection IP pour les unités réactives de gr3n pour la dépolymérisation
- Optimisation supplémentaire grâce à l’analyse avancée des données
- Intégration OT-IT se traduisant par de nouvelles opportunités dans la chaîne de valeur
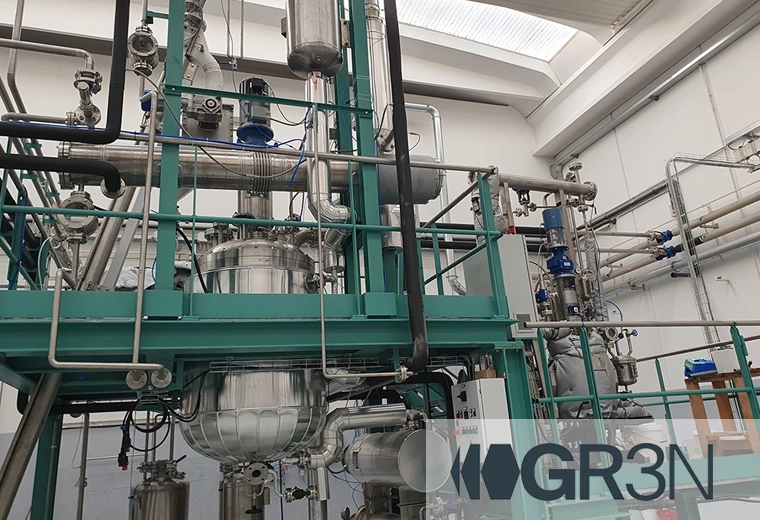
Détails
- Les commandes de l’unité de réacteur sont conçues comme un objet d’automatisation intelligent et indépendant du fournisseur
- L’objet comprend non seulement l’automatisation du processus et l’IHM, mais aussi des services informatiques tels que Track & Trace
- Le processus propriétaire de Gr3n est mis en œuvre dans 6 sections fonctionnelles (Unité – 100 à 600)
- 40 cuves en 4 matériaux différents
- 7 échangeurs de chaleur
- 4 réchauffeurs électriques à huile Diathermic
- Vannes automatiques :
- 73 On-Off (pneumatiques et électriques)
- 6 vannes de contrôle (pneumatiques)
- 40 moteurs (28 variateurs de vitesse)
- 128 capteurs (température, pression, débit, poids, niveau, etc.)
- 4 unités emballées entièrement intégrées
- Environ 500 E/S
- 9 armoires de commande
- Spécifications de contrôle conçues selon la norme ISA-88
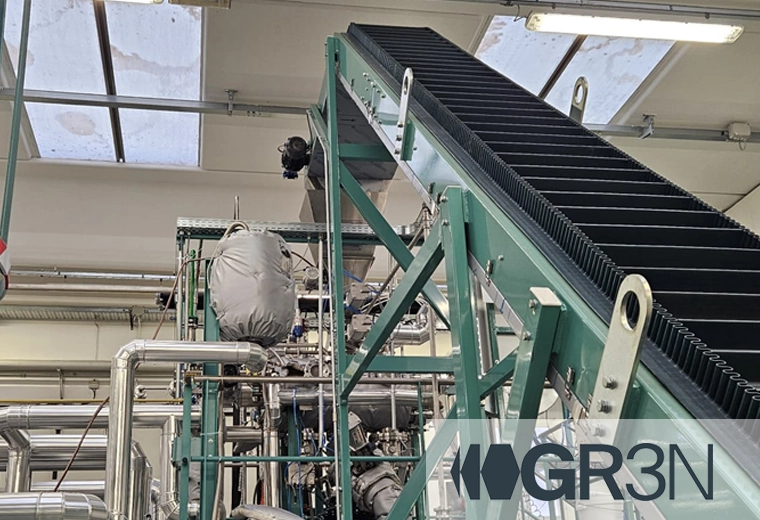
ASRock Industrial & Aimirim
Défi
British American Tobacco était confronté à des inefficacités opérationnelles dans ses usines de fabrication, notamment des arrêts fréquents des machines et une qualité de produit inégale.
Avantages
La mise en œuvre du dispositif d’IA embarqué iEP-6010E d’ASRock et du logiciel Shaman d’Aimirim a permis :
- Un contrôle des processus en temps réel
- Une maintenance prédictive
- Une amélioration de l’évolutivité de l’automatisation
- Une réduction des arrêts de machines
- Une qualité de produit constante
Détails
ASRock Industrial a collaboré avec Aimirim pour déployer une solution basée sur l’IA. Les agents IA ont fourni des recommandations instantanées et intelligentes pour remédier aux inefficacités de la production, garantissant ainsi des opérations plus fluides et une plus grande efficacité.
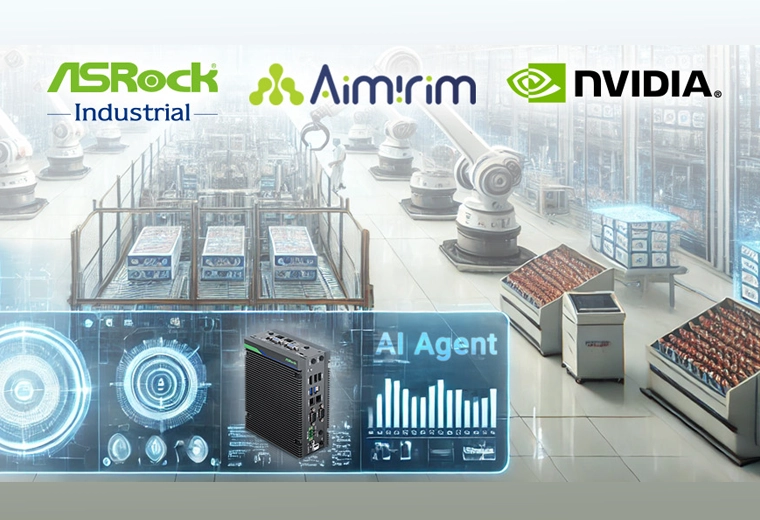
E2COMATION
Défi
Les industries manufacturières sont confrontées à un besoin urgent d’améliorer leur durabilité et leur efficacité énergétique. Cela nécessite une gestion et une analyse efficaces des énormes quantités de données liées à l’énergie générées par des environnements de production de plus en plus complexes.
Avantages
- Amélioration de la performance énergétique et de la durabilité dans le secteur manufacturier.
- Amélioration de la prise de décision grâce à l’analyse et à la prévision des données en temps réel.
- Optimisation des processus de production grâce à la simulation et à la surveillance.
Détails
Le projet s’appuie sur des outils et des méthodologies avancés pour améliorer la performance énergétique et la durabilité dans le secteur manufacturier.
- Energy Monitoring (EMon) : collecte et analyse les données provenant de capteurs.
- Protocole MQTT : facilite la communication entre les appareils.
- APAMA Stream Analytics : analyse les flux de données pour prévoir les performances.
- Digital Twin : simule et surveille les processus de production à des fins d’optimisation.
Financé par l’Union européenne
MODUL4R
Défi
Adapter les systèmes de fabrication à l’évolution rapide des demandes des clients et aux perturbations de la chaîne d’approvisionnement.
Avantages
- Résilience et flexibilité accrues de la production.
- Intégration améliorée avec le métaverse industriel.
- Autonomisation de la main-d’œuvre grâce à l’amélioration des compétences et aux technologies centrées sur l’humain.
Détails
Le projet MODUL4R vise à faire progresser la fabrication grâce à des lignes de production modulaires robustes et autonomes et à des chaînes d’approvisionnement résilientes. Le projet vise à soutenir la production en petites séries et l’adaptation rapide à des situations imprévues.
- Résilience : capacité d’adaptation à des conditions de marché et d’approvisionnement dynamiques.
- Technologies modulaires : opérations de fabrication flexibles et évolutives.
- Simulation et interfaces : intégration avec des environnements numériques tels que le métaverse industriel.
- Technologies centrées sur l’humain : formation et perfectionnement des travailleurs pour les rôles de fabrication modernes.
Financé par l’Union européenne
METAWAVE
Défi
Transformer les processus de chauffage industriel à haute température pour les rendre plus efficaces sur le plan énergétique et plus durables sur le plan environnemental.
Avantages
- Efficacité : réduction de la consommation d’énergie.
- Durabilité : réduction des émissions de gaz à effet de serre.
- Productivité : augmentation du rendement grâce à des technologies innovantes basées sur les micro-ondes.
- Intégration : meilleure optimisation des processus grâce à l’utilisation d’énergies renouvelables et de systèmes numériques.
Détails
Le projet METAWAVE vise à révolutionner les processus de chauffage industriel à haute température à l’aide de systèmes de chauffage par micro-ondes. Il cible des secteurs tels que la céramique, l’asphalte et l’aluminium, et démontre les avantages de ces technologies dans des environnements industriels réels.
- Efficacité énergétique
- Réduction des émissions
- Amélioration de la productivité
- Intégration des énergies renouvelables et des technologies numériques
Financé par l’Union européenne
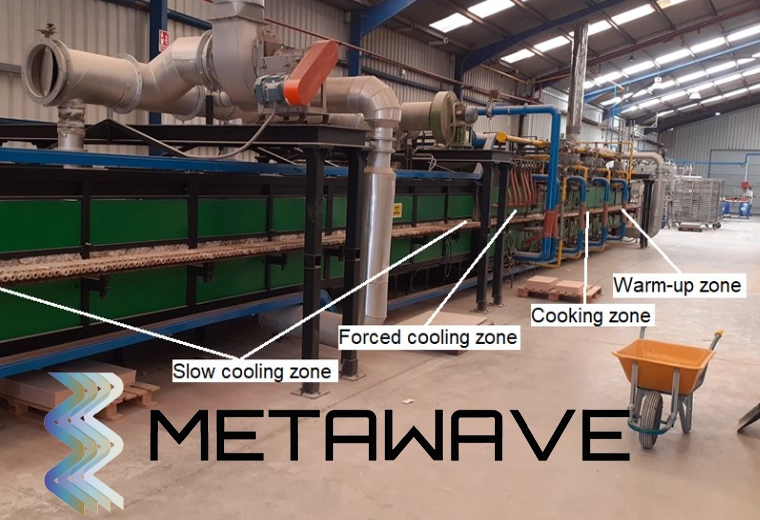
Détection automatique avec Hovering Solutions
Défi
- Les environnements difficiles entravent le déploiement de systèmes autonomes
- La configuration manuelle est lente et source d’erreurs
- Détection des anomalies en temps réel et collecte efficace des données nécessaires
Avantages
- La détection en temps réel renforce la sécurité
- La découverte automatique réduit les coûts de déploiement
- Accélération des données et des missions dans les opérations souterraines
Détails
- IEC 61499 + mDNS/MQTT pour la découverte automatique et la communication
- Drones HSOL avec capteurs IceBlock et détection des anomalies
- Flexbridge permet un déploiement plug-and-produce et évolutif
- Essaim autonome avec localisation et communication sans fil
Intégrateurs technologiques UAO
En cas de besoin de soutien pour intégrer la technologie de l’UAO, voici la liste des membres de l’UAO qui peuvent vous aider.
Dans tous les cas, vous pouvez toujours nous contacter.
Mondial | Accenture | |
Actemium | ||
AFRY | ||
Aimirim | ||
Barbara IoT S. L. | ||
Platinum Electrical Engineering Limited | ||
Schneider Electric | ||
Wood | ||
Yokogawa | ||
Asie-Pacifique | Chine | AutoDriver |
TenLink | ||
Malaisie | TriSystems Engineering | |
Corée, Sud | DhandyMecha | |
ISAAC Engineering | ||
L’Europe | France | Armony System |
Fare Ingénierie | ||
Master Systèmes | ||
Irlande | NeoDyne | |
Italie | J&W | |
Pays-Bas | ICT Netherlands B.V. | |
Suisse | Onify | |
Turquie | KPI Automation | |
UK | AAC Limited | |
Bilfinger | ||
BPX Electromechanical Co Ltd | ||
Ematics | ||
INDEFF | ||
Laplace Control Solutions | ||
Amérique du Nord | USA | Crescent Electric Supply Company |
ENGlobal U.S. Inc | ||
Enterprise Automation | ||
Graybar Electric Company Inc | ||
Mayer Electric Supply | ||
Radical Inginuity Group | ||
RoviSys | ||
Summit Electric Supply | ||
Upstate Automation | ||