Use Cases
How our members use UAO technology and how this benefits business value.
—
If you’re interested in LAUNCHING A PROJECT with UAO TECHNOLOGY and would like some support, we would love to hear from you!
ExxonMobil
Challenge
Adopt an open platform to not be locked to a single vendor
Benefits
- Portability of applications using best-in-class software components from different suppliers
- Executing control applications and control logic consistent with Open automation standards
- Reduce engineering & commissioning time
- Boost innovation using proven-in-use software
- Continuous improvement enabled by swapping out existing components with improved ones using standard interfaces
Details
- Using UAO runtime execution engine in Open Process Automation (OPA) test bed since 2018
- Executing a field deployment to replace existing DCS/PLC’s with OPA based system
- Project scope includes 800 IO points, 90+ loops, UAO runtime + OPC UA
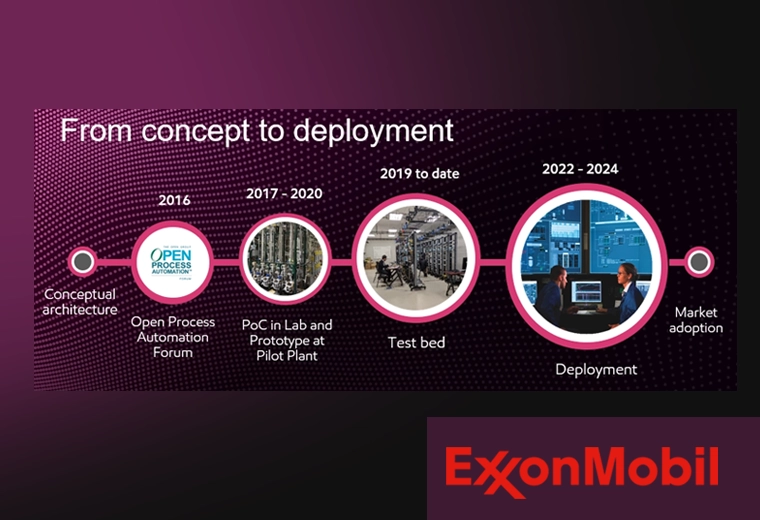
Gr3n
Challenge
Easily expand production using modular mechanical/electrical/control components. Stay the owned of the software intellectual property and gain in flexiblity with regards to the choice of supplier.
Benefits
- Modular engineering of plant automation according to process modularity
- Reduction of engineering costs during market scale-up
- Improvement of TCO for automation in their plants
- New IP protection routes for gr3n’s Reactive Units for depolymerization
- Additional optimization by means of advanced Data Analytics
- OT-IT integration translating into new value chain opportunities
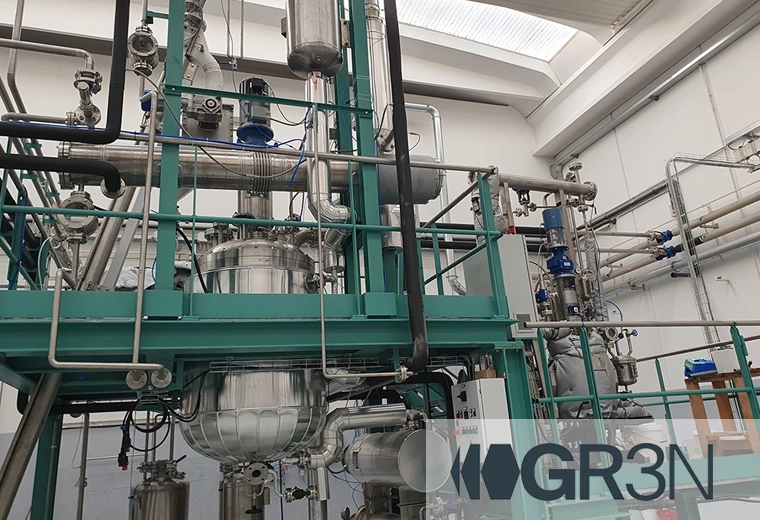
Details
- Reactor unit controls designed as an intelligent vendor-independent automation object
- Object includes not only process automation & HMI, but IT services such as Track & Trace
- Gr3n’s proprietary process implemented in 6 functional sections (Unit – 100 to 600)
- 40 Vessels in 4 different materials
- 7 Heat exchangers
- 4 Diathermic oil electrical heaters
- Automatic Valves:
- 73 On-Off (pneumatic and electric)
- 6 Control Valves (pneumatic)
- 40 Motors (28 Variable Speed Drivers)
- 128 sensors (temperature, pressure, flow-rate, weight, level, etc.)
- 4 Fully integrated packed units
- About 500 I/Os
- 9 control cabinets
- Control Specifications designed according to ISA-88 standard
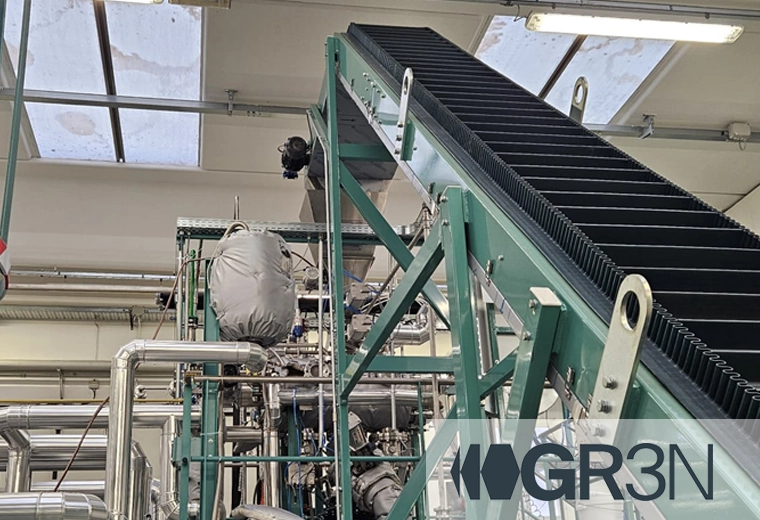
ASRock Industrial & Aimirim
Challenge
British American Tobacco faced operational inefficiencies in their manufacturing facilities, including frequent machine stoppages and inconsistent product quality.
Benefits
The implementation of ASRock’s iEP-6010E edge AI device and Aimirim’s Shaman software led to:
- Real-time process control
- Predictive maintenance
- Improved automation scalability
- Reduced machine stoppages
- Consistent product quality
Details
ASRock Industrial collaborated with Aimirim to deploy an AI-driven solution. The AI agents provided instant, intelligent recommendations to address production inefficiencies, ensuring smoother operations and higher efficiency.
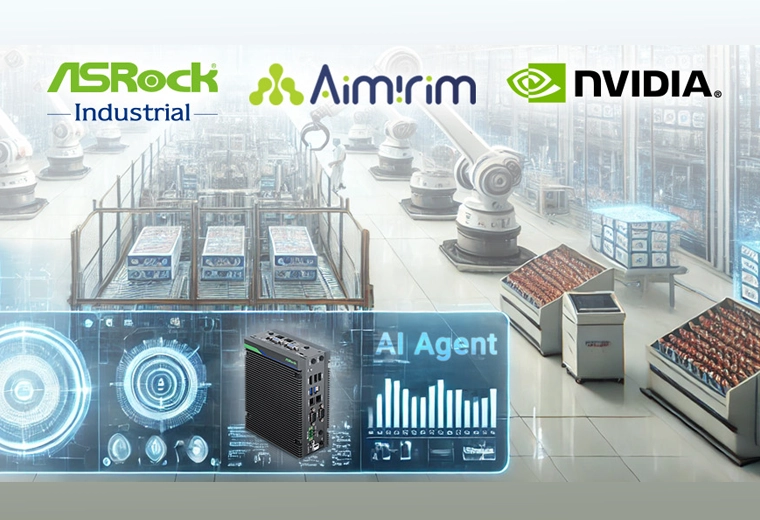
J&W Smart Logistics Center with ASRock Industrial
Challenge
Manual processes led to errors, delays, and low throughput. The system was inflexible and poorly integrated, making updates slow and decision-making inefficient.
Benefits
- Increased operational efficiency and scalability.
- Reduced error rates and labor dependency.
- Future-ready flexibility with modular, reconfigurable logic.
- Improved energy efficiency and system uptime
Details
J&W implemented a hybrid automation system using ASRock Industrial’s iEP-5000G Industrial IoT Controller running IEC 61499 from UniversalAutomation.org.
The system includes:
- Human-cobot collaboration at picking stations.
- Modular conveyor loops with smart sensors and RFID/NFC readers.
- Vision-based control gates for real-time item recognition.
- Autonomous Mobile Robots (AMRs) for bin transport.
- A maintenance station for non-disruptive system updates.
The infrastructure enables real-time coordination across all components.
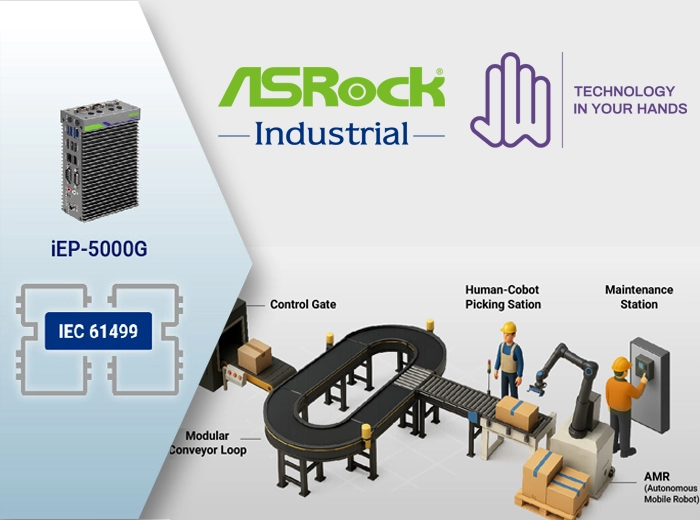
E2COMATION
Challenge
Manufacturing industries face the urgent need to enhance sustainability and energy efficiency. This requires effectively managing and analyzing vast amounts of energy-related data generated by increasingly complex production environments.
Benefits
- Improved energy performance and sustainability in manufacturing.
- Enhanced decision-making through real-time data analysis and forecasting.
- Optimization of production processes via simulation and monitoring.
Details
The project leverages advanced tools and methodologies to enhance energy performance and sustainability in manufacturing.
- Energy Monitoring (EMon): Collects and analyzes data from sensors.
- MQTT Protocol: Facilitates communication between devices.
- APAMA Stream Analytics: Analyzes data streams for performance forecasting.
- Digital Twin: Simulates and monitors production processes for optimization.
Funded by the European Union
MODUL4R
Challenge
Adapting manufacturing systems to rapidly changing customer demands and supply chain disruptions.
Benefits
- Increased resilience and flexibility in production.
- Enhanced integration with the Industrial Metaverse.
- Empowered workforce through upskilling and human-centered technologies.
Details
The MODUL4R project focuses on advancing manufacturing through robust and autonomous modular production lines and resilient supply chains. The project aims to support low-volume production and rapid adaptation to unexpected situations.
- Resilience: Adaptability to dynamic market and supply conditions.
- Modular Technologies: Flexible and scalable manufacturing operations.
- Simulation and Interfaces: Integration with digital environments like the Industrial Metaverse.
- Human-Centered Technologies: Training and upskilling workers for modern manufacturing roles.
Funded by the European Union
METAWAVE
Challenge
Transforming high-temperature industrial heating processes to be more energy-efficient and environmentally sustainable.
Benefits
- Efficiency: Reduced energy consumption.
- Sustainability: Lower greenhouse gas emissions.
- Productivity: Enhanced output through innovative microwave-based technologies.
- Integration: Better process optimization using renewable energy and digital systems.
Details
The METAWAVE project aims to revolutionize high-temperature industrial heating processes using microwave-based heating systems. The project targets sectors like ceramics, asphalt, and aluminum, demonstrating the benefits of these technologies in real industrial settings.
- Energy efficiency
- Emission reduction
- Productivity improvement
- Integration of renewables and digital technologies
Funded by the European Union
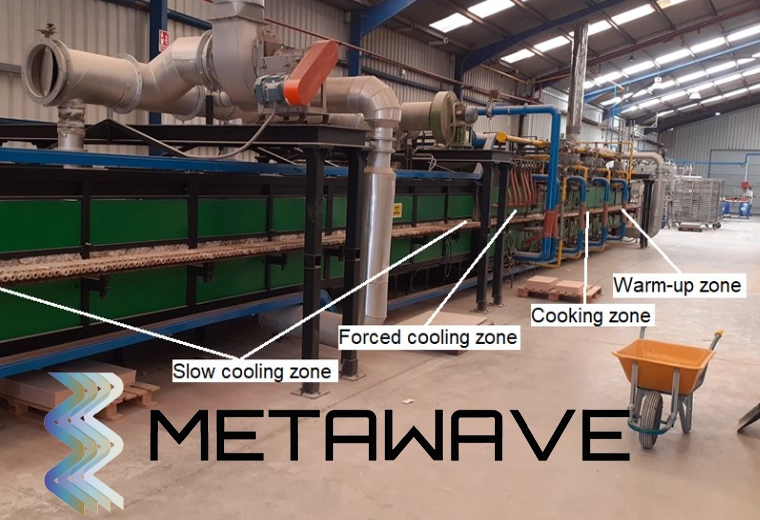
Autodiscovery with Hovering Solutions
Challenge
- Challenging environments hinder autonomous system deployment
- Manual setup is slow and error-prone
- Real-time anomaly detection and efficient data collection needed
Benefits
- Real-time detection boosts safety
- Auto-discovery cuts deployment costs
- Faster data & missions in underground ops
Details
- IEC 61499 + mDNS/MQTT for auto-discovery and communication
- HSOL drones with IceBlock sensors and anomaly detection
- Flexbridge enables plug-and-produce and scalable deployment
- Autonomous swarm with localization and wireless communication
UAO Technology Integrators
In case of support needed to integrate the UAO tehnology, here is the list of UAO members who can support you.
In any case, you can always contact us.
Contact us
Global | Accenture | |
Actemium | ||
AFRY | ||
Aimirim | ||
Barbara IoT S. L. | ||
Platinum Electrical Engineering Limited | ||
Schneider Electric | ||
Wood | ||
Yokogawa | ||
Asia Pacific | China | AutoDriver |
TenLink | ||
Malaysia | TriSystems Engineering | |
Korea, South | DhandyMecha | |
ISAAC Engineering | ||
Europe | France | Armony System |
Fare Ingénierie | ||
Master Systèmes | ||
Ireland | NeoDyne | |
Italy | J&W | |
Netherlands | ICT Netherlands B.V. | |
Switzerland | Onify | |
Turkey | KPI Automation | |
UK | AAC Limited | |
Bilfinger | ||
BPX Electromechanical Co Ltd | ||
Ematics | ||
INDEFF | ||
Laplace Control Solutions | ||
North America | USA | Crescent Electric Supply Company |
ENGlobal U.S. Inc | ||
Enterprise Automation | ||
Graybar Electric Company Inc | ||
Mayer Electric Supply | ||
Radical Inginuity Group | ||
RoviSys | ||
Summit Electric Supply | ||
Upstate Automation | ||